Low cost reflector moulds
Programme: | TRP Workplan | Achieved TRL: | 3 |
Reference: | T524-301MS | Closure: | 2016 |
Contractor(s): | Airbus DS (ES), Univ. Girona (ES) |
The carbon fibre based antenna reflectors are currently manufactured with an autoclave process using Invar moulds. The Invar moulds are specific for each reflector geometry and they are used only once. On the contrary, the surface of the hybrid tools can be easily adapted to different geometries, by re-machining or adding material. This flexibility allows that the hybrid tools can be used several times, in different curing cycles, allowing the production of numerous reflectors.
Objectives:
The aim of the project was to look for alternative moulding solutions to produce antenna reflectors for satellite application.
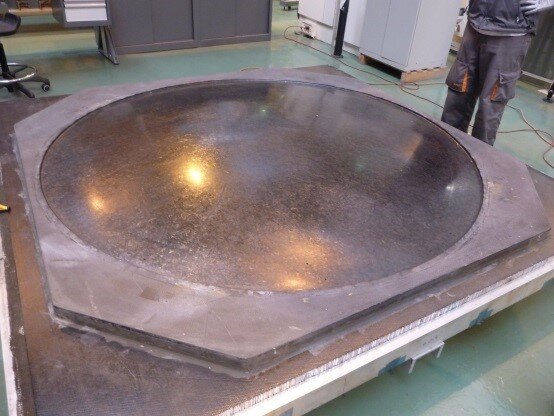
Achievements:
- A review of the literature about moulding tools and different materials has been done.
- New materials and structural concepts have been characterized.
- A hybrid tool has been designed, manufactured, inspected and used for the manufacturing of a full scaled part.
- The main performances of the tool are RMS (Root mean square) =60µm and very good surface quality.
- An antenna reflector has been produced by using this hybrid mould, with RMS=250µm.
- The main conclusion is that new materials have been used, handled and characterized, and a new tooling concept has been proved. Although the final objective may have not been completely achieved (to develop a tooling with equivalent performances of traditional Invar tool), the improvements and changes to the design have been identified and this opens the door to the implementation of this concepts for other types of reflectors.
Benefits:
The capability of reusability makes this concept of mould economically attractive.
Further work:
Improve thermo-elastic modelling of the mould behaviour during curing process and update mould design accordingly.